Resilient Manufacturing: Embedding Quality with Leadership and Technology
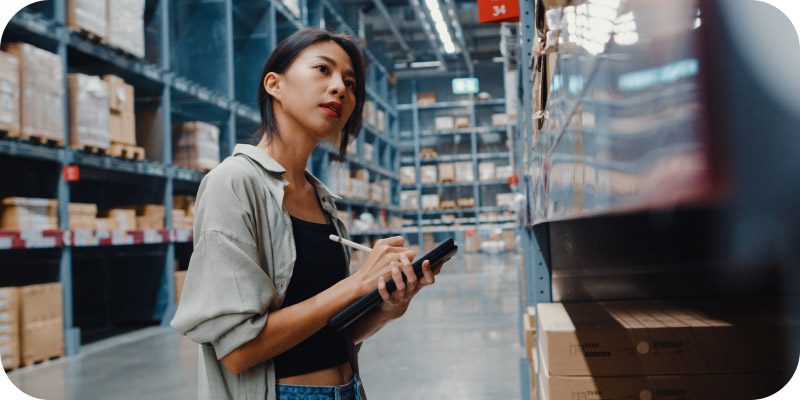
Brian Martensen, Product Manager at Plex, by Rockwell Automation, explains why quality control and management are essential to resilient manufacturing processes. This article originally appeared in Insight Jam, an enterprise IT community that enables human conversation on AI.
As consumer expectations and demand continue to rise, achieving quality in product development isn’t just a goal for manufacturers to achieve—it’s the foundation of the business. Recalls and costly delays plague businesses that fail to go the distance and many high-profile moments in recent years have proven to be case studies on what not to do. The costs of not achieving quality go beyond delays.
When quality standards slip, the financial, reputational, and operational costs are enormous. On the other hand, high-quality standards drive customer satisfaction, protect brand reputation, and ensure long-term profitability. Yet achieving these standards isn’t simple, especially in an environment defined by supply chain complexities, evolving customer demands, and the rapid pace of digital transformation.
The challenge for manufacturers is clear: How do you embed quality into the DNA of your organization while navigating these complexities? The answer lies in the intersection of leadership and technology. Quality must start from the top of leadership, setting an example by leveraging solutions that empower teams, streamline processes, and transform quality management into a strategic advantage.
For the second year in a row, a recent survey of manufacturers found that “improved quality” was the top outcome manufacturers and leaders hope to achieve from existing smart manufacturing technology. This consistent priority signals a broader industry trend: quality must be at the core of the business strategy to drive operational success.
From Compliance to Culture: Technology’s Role in Quality
Traditionally, manufacturers have often viewed quality management through the lens of compliance to meet regulatory standards and avoid penalties. However, the modern manufacturer knows that true excellence requires going beyond compliance to build a culture of quality. This culture is not just about checking boxes. It’s about continuous improvement and a shared commitment to delivering exceptional products and services. Smart manufacturing technologies, like digital quality management systems (QMS), are key to enabling this shift. These tools provide real-time data, actionable insights, and the ability to address potential quality issues before they escalate. However, technology must be combined with leadership and strategic implementation to help establish an environment that prioritizes quality at all levels.
Quality isn’t just the responsibility of one team—it requires cross-functional collaboration. But it also must start from the top. Leaders play a key role in modeling this culture of quality by demonstrating the importance of excellence in every decision and action. They must also set measurable goals, foster open communication, and build trust. In addition to fostering a collaborative, quality-focused mindset among teams, leaders can also champion smart manufacturing solutions that ensure collaborative teams can achieve quality goals by tracking their progress toward these goals in real-time.
This technology can also break down organizational silos by centralizing data and fostering seamless communication. For example, a food manufacturer leveraging a QMS system can monitor production quality in real-time. Automating defect detection and leveraging predictive analytics helps the company reduce waste, minimize recalls, and maintain compliance with industry standards. This real-time visibility helps them improve their efficiency, lower their costs, and build trust with customers by consistently creating quality products.
Building a Quality-Driven Culture
Creating a culture of quality begins with leadership but is sustained through the strategic use of technology. Here are four key strategies manufacturers can adopt:
Define Clear Quality Objectives
Leadership must set measurable quality goals that align with broader organizational objectives. For example, instead of simply aiming to “reduce defects,” a manufacturer could set a specific target to reduce defect rates by 20 percent within a year.
Invest in Training and Empowerment
Technology is only as effective as the people using it. Regular training and access to digital tools aren’t just perks—they’re essential. Instruction and practice are key to ensuring employees are equipped with smart manufacturing tools and understand how their roles impact quality outcomes. Leaders should invest in intuitive platforms and provide employees with the resources they need to make data-driven decisions.
Foster Collaboration Across Departments
Effective quality management is not limited to quality control or production teams. A culture of quality thrives with cross-functional collaboration. Tools like collaborative ERP systems foster communication between departments, breaking down barriers and enabling a more holistic approach to quality management. For example, when production and procurement teams share real-time data on material quality, they can quickly address issues before they escalate.
Empower Continuous Improvement
Continuous improvement is at the heart of a thriving quality culture. Leaders must create systems that empower employees to share ideas, identify inefficiencies, and propose solutions—all with the support of real-time data and actionable insights. By leveraging modern IT tools to establish transparent feedback loops, organizations can proactively evaluate and refine processes while encouraging employee engagement.
The Future of Manufacturing: A Technology-Driven Culture of Quality
As manufacturing continues to evolve and grow in complexity, organizations that embrace technology to build a culture of quality will lead the industry. These companies will not only meet customer expectations but exceed them, setting new standards for excellence. The result is a resilient, future-ready organization prepared to thrive in a shifting industry. In the end, a culture of quality isn’t just about avoiding mistakes. It’s about delivering value, fostering trust, and achieving long-term success. Businesses that combine leadership with the right technology solutions can transform quality management into a strategic advantage.