Workflow Automation for Manufacturing: It Doesn’t Have to be All or Nothing
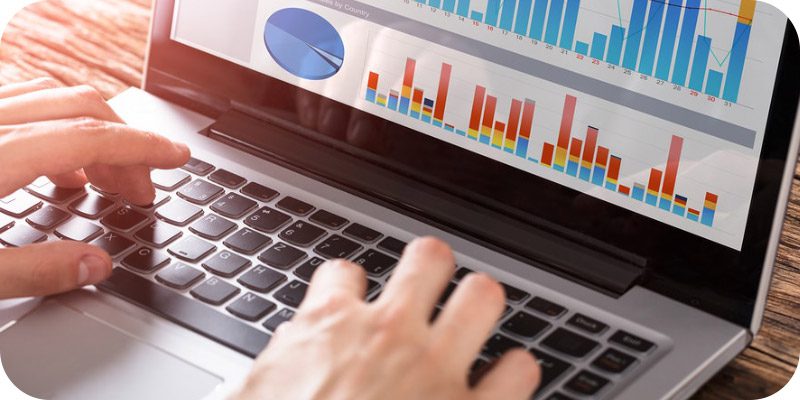
Josh Roth, the General Manager U.S. for Pipefy, explains why workflow automation for manufacturing doesn’t have to be “all or nothing.” This article originally appeared in Insight Jam, an enterprise IT community that enables human conversation on AI.
We all know people with an “all or nothing,” “now or never,” or “sink or swim” approach to life. While it may be impressive in a football game or the climax of a movie, the truth is an “all or nothing” mindset glorifies extremes with no middle ground. In business, implementing new technologies—even when transformative to your operation—can seem like an “all or nothing” proposition. The undertaking may appear overwhelming, but it doesn’t have to be if taken step by step. For manufacturing, workflow automation can immediately produce benefits, even based on automating small processes and building from there.
Overall, manufacturing businesses have done an excellent job modernizing factory floor operations. Unfortunately, beyond the floor, many front—and back-office workflows are still painfully slow, disjointed, and prone to countless errors. A company’s lack of workflow automation can negatively impact even the most impressive factory floor innovations.
First, let’s break down the problem many manufacturers face: their workflow process functions in some fashion—usually through a messy series of emails, spreadsheets, side discussions, and managers’ memories. Although imperfect, the operation is so entrenched that management fears breaking down the current system. But sometimes, you need to step away from the day-to-day operation and take an honest look at it.
The steps involved in a single manufacturing transaction may go from purchase requisition to manager approval, supplier outreach, budgeting, setting a delivery date, organizing production, ensuring quality control, and engineering. You can see how many vulnerable gaps exist if the workflow process is disjointed. A manager may forget to note a deadline, or an important email may be overlooked or sent to the wrong email. Many manufacturing businesses are sacrificing speed, efficiency, and improved quality control for the status quo, even with emerging technology solutions that can significantly transform operations.
To address this workflow disconnect between departments and functions, it is of the utmost importance to recognize that quality control is key. Little errors along the way can become big and disastrous in the end. Your business may have been lucky so far, but relying on old processes is riskier than biting the bullet and switching to automating workflow processes. Additionally, cost and time savings gained by automating workflows are huge bonuses to the operation and the bottom line.
For example, a major supplier in the energy segment recently adopted a workflow automation solution that reduced its turn-around time from 90 days to less than a week. They were able to scale faster while also significantly decreasing production errors. For this company, all areas—from the front office to the back office and the factory floor—were connected with workflow automation so that orders could move rapidly and accurately through measurement, purchase, and production.
The supplier was concerned with disrupting the business, so they started small by automating quality assurance first and then adding purchasing and maintenance requests. By automating quality assurance into a paperless process that used to be piles of paper, the manufacturing company can now easily trace the status and quality of all the parts it produces. By using a no-code AI-driven solution, the teams could quickly build workflows customized to their operation and/or tasks, and they could make changes easily as they gradually added more processes. By not relying solely on their IT to implement the solution, this approach was faster and easier to implement.
Many manufacturing companies find that the easiest tasks to automate first are the most repetitive, manual processes, such as purchasing and maintenance requests. After automating a few tasks, you can scale quickly and continue to chip away until the entire process is a fully integrated workflow. Truly, any manufacturer will find benefits to rethinking and closely assessing their workflow process so that they can achieve the highest levels of efficiency and product quality.
Don’t let “all or nothing” thinking prevent your manufacturing company from transforming to workflow automation. Take the first step, and you will soon be running full speed and never looking back.