A Business Case for Digitizing Manufacturing Maintenance and Inspection Processes
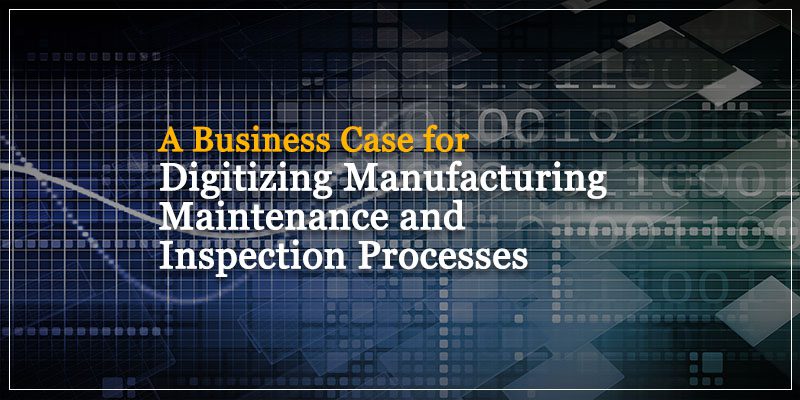
As part of Solutions Review’s Contributed Content Series—a collection of articles written by industry thought leaders in maturing software categories—Cris Grossmann, the CEO at Beekeeper, makes a business case for digitizing your manufacturing maintenance and inspection processes.
As a teenager, I remember accompanying my grandfather to work at the town copper factory. As members of the quality assurance team, we polished the equipment used to produce copper strips so that new products would not have any marks on them. We used handwritten notes to track upcoming and completed tasks and facilitate shift handovers.
It’s not surprising that things fell through the cracks with this system. One day, I misread a note left by a worker on a previous shift. That simple error caused me to make a maintenance mistake. As a result, all of the copper strips produced that morning failed to meet quality standards. The company had to shut down a production line for almost three hours to fix the issue, which was a stressful experience for everyone involved, especially me.
The manufacturing industry has changed significantly since I worked side-by-side with my grandfather. However, many companies still use legacy manual processes to inspect and maintain equipment. These outdated processes are failing companies, preventing frontline workers from doing their best work, and costing businesses significant sums. The hidden costs of using paper-based maintenance and inspection processes include human errors, equipment breakdowns, lost production, sunk labor costs, quality issues, lower revenues, greater worker safety incidents, and decreased customer satisfaction.
Researchers from the National Institute of Standards and Technology (NIST) estimate that U.S. discrete manufacturers’ total annual costs associated with maintenance average $222 billion a year, with sales losses accounting for nearly half of this total. At the same time, 50 percent of respondents rely on reactive maintenance, and another 50 percent use predictive and preventive maintenance to optimize their business. This second group experienced 52.7 percent less unplanned downtime and 78.5 percent fewer defects due to their advanced processes. Results are likely to be even more compelling for manufacturers of high-cost goods as maintenance costs represent up to 70 percent of the cost of finished items, NIST researchers state.
Digitize Your Paper Maintenance and Inspection Processes
These results provide a real-world business case for digitizing maintenance, inspection forms, and checklists. By digitizing these processes with connected workforce applications, manufacturers can significantly reduce errors and inconsistencies and decrease unplanned outages that harm productivity and revenues. And if companies need more evidence, consider this: the cost of unplanned downtime is 50 percent greater now than it was in 2019-2020 due to skyrocketing inflation and higher-capacity production lines. Fortune Global 500 industrial companies will lose $1.5 trillion to unplanned downtime this year—or 11 percent of their revenues, finds a survey from Senseye Predictive Maintenance.
The cost of a lost hour of production now ranges from $39K for fast-moving consumer goods (FMCG) facilities to more than $2M for automotive plants. Major manufacturers are experiencing 20 monthly unplanned downtime incidents per facility. While that’s six fewer than two years ago, these incidents take longer to recover from, meaning that plants have only gained two extra hours of monthly production capacity.
At companies that operate with a break-fix mentality, workers spend their time troubleshooting issues they may not be qualified to address or waiting for production lines to be restored so they can return to work. Companies with lagging maintenance practices will likely experience higher workforce attrition as employees leave to join companies with safer, more predictable operational environments.
Investing in mobile-first tools built for frontline workers that can improve maintenance processes thus makes good business sense. Digital checklists enable staff to work through inspection processes and attest that equipment is in good working order. Employees can digitally submit work orders to maintenance teams when they encounter issues, shortening the time between detection and repairs.
Automated assignments route jobs to the right technicians, ensuring they get all the data they need to schedule inspections and begin work. Managers are kept in the loop and can approve repairs when needed. Digital scheduling and reminders help companies adopt proactive maintenance processes that improve productivity and reduce outages year-round. For example, technicians can conduct proactive maintenance before or after shifts, ensuring that production lines are humming and can drive throughput as each new group of workers arrives.
Digital Maintenance Processes Help Protect Workers On-the-Job
Proactive maintenance also reduces the prospect of worker injuries and fatalities on the job. According to the Bureau of Labor Statistics, fatal workplace injuries increased in the U.S. by 8.9 percent from 2020 to 2021, with 5,190 fatal work injuries occurring in 2021. A second NIST study attributes 134.9 on-the-job injuries at manufacturing plants to reactive maintenance, meaning they likely could have been entirely avoided with better practices.
Teams can use frontline success systems to schedule and routinely perform safety audits, ensuring that production materials and chemicals are stored and used safely, and that equipment performs as expected. When issues arise, frontline workers can escalate issues for resolution and prioritize repairs to mitigate risks. Managers can view analytics, such as maintenance backlogs and time-to-repair, indicating a need to add more staff or authorize extra hours to complete critical tasks.
Conducting proactive manufacturing maintenance improves workplace safety, increases morale, and protects companies from lawsuits and expensive payouts. Manufacturers can provide on-demand safety records and show analytics demonstrating their work to reduce risks and keep workers safe, ensuring compliance with relevant regulations.
The Evidence Is that Proactive Maintenance Improves Business Results
Frontline success systems help companies create best-in-class inspection, manufacturing maintenance, and safety programs. Workers can easily access data, forms, and records to complete tasks, while digital workflow improves consistency, speeds processes, and creates better business results. Manufacturers that move from reactive to proactive maintenance improve production, revenues, and reliability while protecting frontline workers and creating a safe workplace environment. With these results, investments in frontline success systems often pay for themselves.