The U.S. Port Strike Highlights Three Tech Lessons for Supply Chains
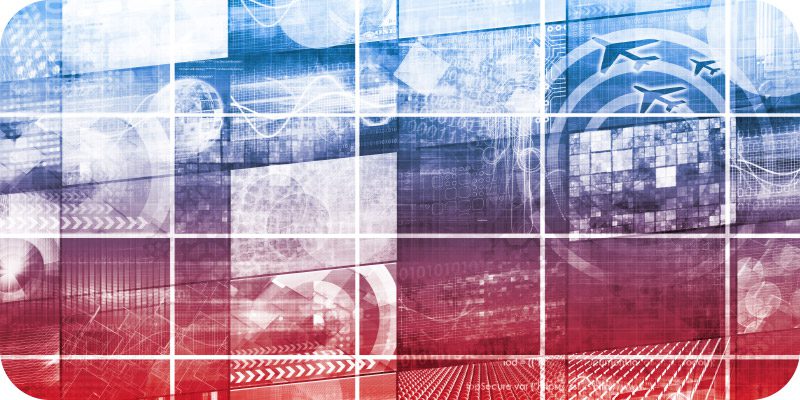
Paul Bellamy, a logistics leader at Genpact, explains how the U.S. port strike highlights three tech lessons companies should apply to their supply chains. This article originally appeared in Insight Jam, an enterprise IT community that enables human conversation on AI.
Every so often, a major news event occurs that underscores the importance of data and analytics in helping companies become more agile and, in turn, keep prices at reasonable levels for the end consumer. Earlier this month, this came from the U.S. port strikes.
After dockworkers across the Eastern seaboard hit the picket lines, retailers and suppliers scrambled to ensure they could keep products and materials moving and avoid skyrocketing shipping costs. Fortunately, the ports reopened only three days after the strike began, narrowly avoiding a significant crisis leading up to the presidential election and busy holiday shopping season.
While the worst was avoided, retailers, suppliers, and shippers should learn a few lessons from this near-calamity—and those who do will be much better prepared to withstand the next supply chain snarl.
Having a robust simulation plan in place is crucial
In a perfect world, shippers would have begun simulating the potential impacts of the port strikes weeks or months before the shutdown. Creating a contingency plan rooted in data and analytics is something all suppliers should prioritize for the next major event.
Some of the most important things to include in simulations of this nature include how goods can be transported out of ports (or, more generally, any locations) facing a shutdown, where containers can be redirected to, and any international considerations they may have. For example, if the dockworker’s strike stretched beyond a few days, suppliers would have needed to consider whether containers coming from Asia and Europe could be redirected to Canadian or Mexican ports in addition to West Coast ports.
These simulations help suppliers uncover specific route guidance to navigate in the immediate days and weeks after an event. Although the International Longshoremen’s Association is back to work, the strike will have ripple effects on the global supply chain for weeks to come, and suppliers with a contingency plan will be able to navigate the redirection of cargo much more smoothly and effectively.
If you don’t have visibility throughout the supply chain, you don’t have a chance
When massive supply chain events occur, a critical factor in suppliers’ ability to adapt is how quickly these changes can be implemented and the cost implications.
Today’s companies must design and run hyperconnected supply chains with data and analytics powered by artificial intelligence (AI) embedded into their workflows. With visibility into the end-to-end supply chain—across plan, source, make, and deliver functions—organizations can respond to disruptions faster and make data-backed decisions to redirect inventory.
Building supply chain resilience is all about having a holistic view of your operations and alternative operational scenarios based on the data to be ahead of the game when problems occur.
Timelines for the holiday season are shifting even further up
Fortunately, leading retailers and suppliers took steps to avoid the strike’s most devastating potential impact: inventory gaps for the holiday shopping season. Many retail industry shippers had already begun moving inventory for the holiday season in August or earlier. Some of the supply chain challenges brought to light by the COVID-19 pandemic encouraged these companies to move up their timelines and play it safe by shipping cargo earlier in the summer.
The shifting of timelines further proves the value of AI for demand forecasting. By sending and receiving products earlier in the year—which means even more uncertainty about how much will be sold in the fall and winter months—companies are taking a more significant risk in accurately predicting demand. With a holistic, AI-powered solution, companies can better predict and adjust to fluctuations in demand to maximize available inventory and sales.
Global supply chains will normalize and move beyond the shorter-term impact of the dockworkers’ strike. However, for the next few weeks, we can expect to see small disruptions caused by cargo backup. By implementing what they’ve learned into their supply chain practices, companies can turn this event into a positive lesson for years to come. If there’s one thing to count on, it’s that another major supply chain disruption will happen at some point in the near future. It seems obvious, but it’s better to prepare now than to react when it does.