Most Important Steps To Good Warehouse Organization (And How Data Helps)
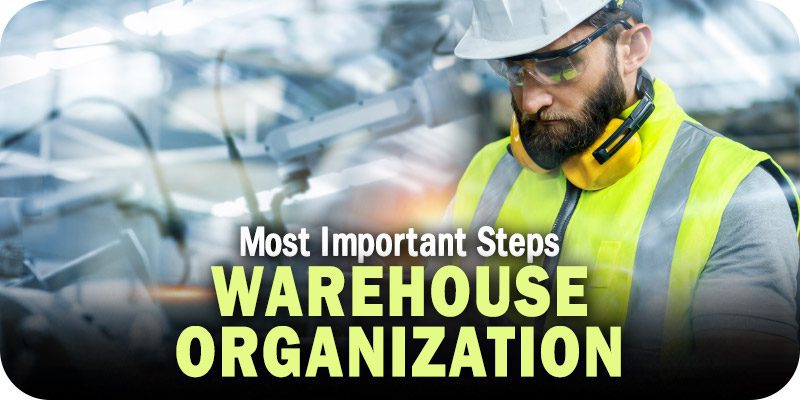
As part of Solutions Review’s Contributed Content Series—a collection of articles written by industry thought leaders in maturing software categories—Alex Selwitz, the Director of SEO for Red Stag Fulfillment, outlines some of the most critical steps in effective warehouse organization.
Errors in storage and order delivery can be catastrophic for a warehousing business. Certainly, you don’t want your goods to be part of the $163 billion lost annually as inventory waste. Whether in a manual or automated warehouse, a key component to success is reducing the margin of error.
In early 2023, Forbes forecasts that 20.8 percent of retail sales will be online, presenting a new challenge for warehouse management. The increased need for warehouses took a new turn in 2020 through 2021 when 79 percent of third-party logistics reported profitability. While that makes starting e-commerce fulfillment services appealing, it also presents unique challenges.
Management systems can easily get overwhelmed with orders, storage, picking, and packing. Here are a few steps to good warehouse management to help you get things under control. We’ve divided them into three categories: setup, storage solutions, and inventory management.
1. Setup the Layout
A good layout optimizes the space, boosts order-picking accuracy, reduces damage, and increases efficiency. Hence the need to get it right from the start. Data is essential in planning the layout. That includes item sizes, number of products, type of products, dispatch frequency, number of employees, and equipment. Collecting and analyzing these should be primary in the layout setup.
However, layout restructuring can be tricky for existing and operational warehouses. Here is what you can do if you already have an existing structure.
Get the total volume of the warehouse.
The total volume of a warehouse tells you how much space you have. Start by measuring the floor area before obtaining the volume. Here’s a simple formula to use for the area and volume:
- Area = length X breadth
- Volume = floor area X height
Uneven flooring will require taking individual volumes for each section. Alternatively, you can use 3D scanning technology.
Set out the floor plan.
You need to designate storage areas and passageways. Also, there must be adequate consideration of safety. That will include planning for guard rails, safety bollards, handrails, rack safety back panels, etc. Local authorities and safety bodies will have standards you must adhere to for approval.
While at it, consider the following
- Storage solution: This refers to racks, pallets, shelves, etc. They can boost efficiency, especially those compatible with forklifts.
- Multi-tier storage: This involves using vertical stacks. They are efficient in space optimization.
- Product Type: Products are often boxed, ranging from lightweight house appliances to heavy spare parts. They help determine the storage solution.
- Picking equipment (order picker, forklift): These equipment determine the speed of loading and offloading from storage. Forklifts can deal with heavier goods and higher heights than order pickers.
You must also consider other automated solutions, which include conveyors, robotic arms, automatic guided vehicles (AGVs), etc. For example, the AGVs require a pre-designed circuit to move around the warehouse. Automated solutions can improve efficiency, reduce error, reduce processing time, etc.
Designate sections based on dispatch frequency.
Speed, from offloading to storage, picking, packaging, and delivery, is essential in warehouse operations. Orders are often time-based, hence the need to fulfill them within the timeframe. One way to hasten processes is to designate sections based on dispatch frequency.
Dispatch data from the inventory management system can help when designating sections. It tells how often products are received and dispatched (order history). The ABC analysis is widely used in inventory management, including supply chain systems. However, it can point the way during the layout. Products in category A contribute to the majority of the movement. Hence, they should be placed closer to the offloading and loading areas. The priority goes down to categories B and C.
These first three steps will set you up for an efficient warehouse organization structure. Keeping things where they need to be is integral to inventory management, which we’ll touch on later.
2. Pick a Storage Solution
A good storage solution should facilitate easy storage and removal of products. Most importantly, it should be suitable for the product type. For example, racks are better for palletted products, while boxed products can go with shelves.
Shelving and racking are the two most common solutions. Their versatility can accommodate various products and storage designs (vertically and horizontally). Information like the product size, dimensions, and weight are essential in determining the most efficient storage solution. Dimensions determine the storage size, while weight determines the material. An example is choosing between a racking system and static shelving.
The frequency of retrieval and stock levels (volume) also determines the storage solution. For example, mobile shelving is most suitable for frequently retrieved products. You can implement them as follows:
Shelving (static & mobile)
Static shelving is typical for manual storage and lightweight products. Also, elevation is often within human reach. A more robust system will be mobile shelving mounted on rails or carriages. The mobile shelving systems allow for easier access in less space. Their motion also helps in loading and unloading. Ultimately, pick them depending on the products and volume.
Choosing which shelving type to use depends on the product size and weight. Visibility and air circulation can also play a deciding role. For example, wire shelving is open with all-around access but only ideal for lightweight items.
Racking (pallet & multi-tier)
Racking is where order pickers and folk lifts come into play. Pallets are the center of these operations as they hold the products, often in large boxes. A forklift unloads them and comfortably stores them on the racks. A multi-tier racking system optimizes storage by adding vertical layers. It is ideal for lightweight items but can be built to carry heavy ones. Pick multi-tier to maximize your space, as you can expand vertically without compromising horizontal space for movement.
3. Manage Inventory
Inventory management is the final step in warehouse organization. It cuts through all warehouse operations processes, including receiving, storing, picking, packaging, and delivery. You’ll need data to manage inventory. A simple barcode scanner sends the code to the software, interpreting and revealing the product details.
An enterprise resource planning software can quickly identify a product leaving or coming into the warehouse. That happens once the barcode or RFID scanners read the data. With that, it is easy to manage the stock levels of your inventory.
Use SKU codes
How do you easily track the same item in different colors? Stock-keeping units (SKU) are codes that identify all the items in your warehouse. They differentiate similar items by their colors, size, etc. Scannable SKUs help track inventory levels. For example, during dispatch, the point-of-sale system scans the SKU of an item and removes it from the inventory.
You decide how to create the SKUs. Nevertheless, avoid using O and 0, as they can be confusing when differentiating between the number and the alphabet. Here is an example of an SKU
- Silver-colored, medium-sized water dispenser: WAT-MED-SL
Apply labels and signage
Labels can be stickers, barcodes, or magnetic signs for location, inventory, and identification. Choose materials (e.g., vinyl, polyester) that maintain legibility (wear-and-tear resistant) for a long time. Ensure labels and signs have zero visual obstructions and use high-contrast colors. Finally, update them when there is any warehouse change.
Conclusion
Warehouse organization begins with the layout. Once you’ve optimized the areas for storage and movement, you can pick the best and most ideal storage solutions. The last step is inventory management. Achieving proper warehouse organization with these steps, especially in the design stage, can boost operations efficiency by 20 to 25 percent. However, Regular maintenance is necessary to maintain it.