The Key Factors Influencing the Rise of Manufacturing Reshoring
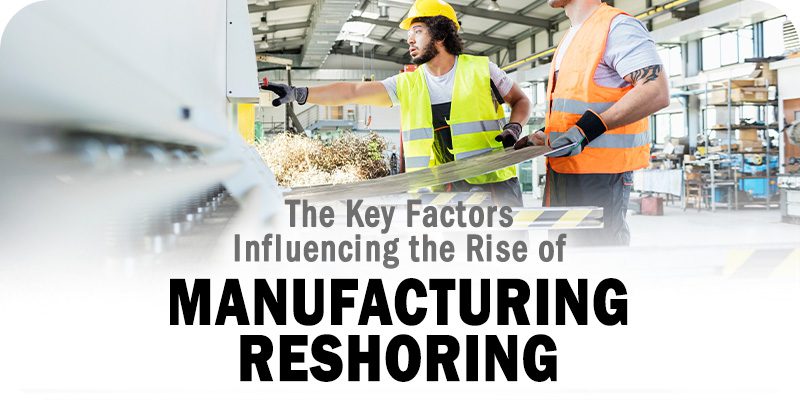
As part of Solutions Review’s Contributed Content Series—a collection of articles written by industry thought leaders in maturing software categories—Maggie Slowik, Global Industry Director for Manufacturing at IFS, explores the key factors influencing the rise of manufacturing reshoring and the positive impacts on a rebound for U.S. manufacturing.
The manufacturing industry has not yet recovered to total capacity since the pandemic caused skills shortages, supply chain issues, and geopolitical problems. To return to pre-pandemic levels, many logistic providers and manufacturers are bringing operations back to home soil.
Reshoring has attracted companies from across the globe. In North America, for example, core reshoring goals include complete control of the supply chain by manufacturing products on home soil. This transition is well underway across the U.S. as research shows in 2022, 350,000 jobs were re-shored back to the U.S.—an increase of almost 100,000 compared to 2021.
Leave Supply Chain and Economic Troubles Behind
Roadmaps are being established across U.S., Indian, and European economies to balance supply chains and increase resiliency, meaning companies will be less dependent on China. Investment from companies building infrastructure and plants in Vietnam and India has increased already as companies look to adopt the China Plus One strategy and source materials from other countries.
Being more self-sufficient, holes in supply chains, and an unpredictable geopolitical climate are all critical reasons for the uptake in restoring, according to the Reshoring Initiative® IH 2022 Data Report. Supply chain disruptions have been an issue since 2020, with 69 percent stating it as their main reason for reshoring.
For example, consider the bipartisan National Development Strategy and Coordination Bill introduced in December 2022. It aimed to highlight how vital manufacturing reshoring was to developing the national economy in the future in 2023. It started a national movement to reinforce supply chains and promote domestic manufacturing.
Sustainability Must Be Factored In When Making the Decision to Re-Shore
Recent research found that 72 percent of senior decision-makers working for large enterprises globally have increased their usage of domestic suppliers compared to international suppliers. From a sustainability perspective, there are considerable benefits to be gained. In fact, reshoring gives manufacturers a golden opportunity to look hard at their manufacturing processes and how they can develop more sustainable processes. It can minimize Co2 emissions as transport is reduced and spur a reduction in wasteful over-production as supply chains are brought closer together. As the world strives to act more sustainably in the race to net zero, environmental benefits will play a massive role in driving new sourcing strategies.
Swings and Roundabouts – Costs Can Spiral
However, the raw materials, components, and products sourced from suppliers will likely become more expensive, especially as inflation continues to increase globally. As a result, the research found that 53 percent of companies have considered increasing the proportion of materials/components they produce in-house. But again, these measures and others like them that organizations are now taking to mitigate risk will likely add cost, complexity, and waste to the supply chain.
So, reshoring is not the silver bullet to mitigate supply chain disruption entirely. Often, companies underestimate the sheer level of effort, costs, and logistical planning required to make reshoring a success. But for many U.S. companies, the extra costs to manufacture within the country are outweighed by saved customs and shipping costs and the additional sustainability benefits associated with offshore operations.
Tech is Eagerly Waiting to Go!
It’s here organizations need the helping hand of technology—in fact, it can be a key facilitator for solving supply chain, labor, and production challenges associated with reshoring. For 94 percent of respondents in a recent McKinsey study, Industry 4.0 helped keep operations running during the COVID-19 pandemic, with another 56 percent claiming Industry 4.0 technologies had been critical for efficient responses.
A new IDC InfoBrief, sponsored by IFS and entitled Shaping the Future of Manufacturing, shows an active correlation between digital maturity and profit—manufacturers reporting an optimized level of digital transformation saw profits increase (40 percent). In contrast, those with less advanced digital transformation maturity suffered bigger reductions in profit in the last fiscal year.
As is often the case, this business conundrum needs the help of technology, and it has been quick to respond to the call to deliver the agility and Time to Insight (TTI) that manufacturers need to better forecast demand and provide a more detailed view of sustainability across product supply chains.
Exceptional supply chain management will be a vital part of the move to reshoring. The IFS study showed that 37 percent of respondents now saw supply chain management as one of the top three priorities their organization is trying to solve through technology investment. The technology is there.
Is the Reshoring Journey Worth Taking?
In a recent Kearney Index, 92 percent of executives had positive opinions about manufacturing reshoring. It’s no surprise to anyone when the additional benefits are considered. It’s not just a protected supply chain ecosystem manufacturers will gain; reshoring also has societal benefits. Reshoring and foreign direct investment (FDI) jobs reached record highs in 2021 after they were propelled by the private and federal push for a domestic U.S. supply of essential goods, according to the U.S. Reshoring Initiative.
Consumers think so
Research shows that 83 percent of U.S. consumers are willing to pay 20 percent more for American-made products, and 57 percent stated that their choice of product could be swayed depending on where the product is manufactured. It’s clear to see there are also profitable and supply chain benefits up for grabs.
When looking at it from a management perspective, you can gain significant control over operations by bringing all operations to one centralized location. This can happen while IoT, AI, and Machine Learning continue to take care of the monotonous tasks. Manufacturers will also gain shorter supply chains, and on-site teams will benefit from reduced time differences, meaning they’ll have better communications across manufacturing plants and headquarters.
A Strong Digital Backbone Will Allow Reshoring to Prosper
To thrive now and in the future, manufacturers must implement reshoring using the correct technology efficiently and cost-effectively. When done correctly, it is clear to see the appeal for U.S.-based manufacturers to address reshoring now and why it’s a fast-emerging trend in the industry.
The journey will not be smooth sailing, but with the strong support of an agile digital backbone, the long-term results of increased employment and greater supply chain control will make the return to home soil safer and more profitable.