Understanding the Difference Between Lean and Six Sigma
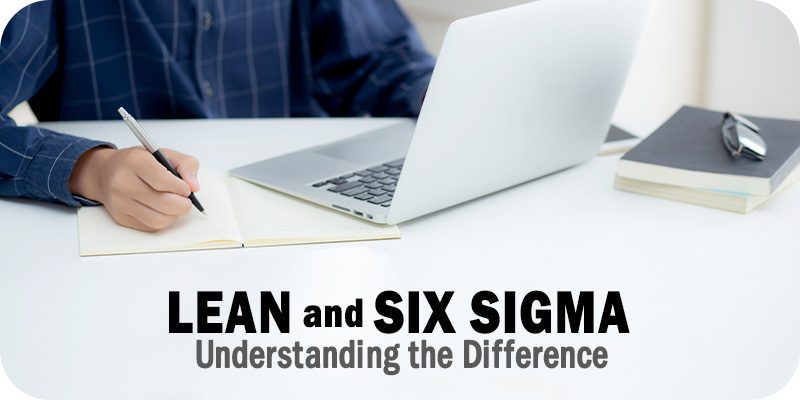
The editors at Solutions Review have defined and summarized the differences between the Lean and Six Sigma methodologies.
In the world of process improvement methodologies, Lean and Six Sigma are two of the most prominent approaches companies use across industries. Lean and Six Sigma enhance organizational performance, increase process efficiency, and reduce waste. While the two methods have similarities and can address similar business needs, it’s essential to understand what makes them different. With that in mind, our editors have defined both methodologies, outlined their differences, and highlighted how they can complement each other.
What is Lean Methodology?
Lean methodology—sometimes known as Lean manufacturing or Lean thinking—is a systematic approach that originated from the Toyota Production System (TPS) and is now used across industries. At its core, Lean focuses on identifying and eliminating activities that don’t add value to the customer. These discarded activities are called “waste,” by reducing the amount of waste in a process, a company can enhance its operational efficiency, quality, and overall productivity.
The foundational principles of the Lean methodologic include:
- Value: Identify the customer’s unique needs and focus on the activities/processes contributing to meeting those needs.
- Value Stream: Map the entire value stream, from initial input to final output. This will help users understand the flow of materials, information, and activities throughout the analyzed process.
- Flow: Ensure uninterrupted workflows by minimizing interruptions, delays, and non-value-added steps.
- Pull: Develop a system where work is pulled based on customer demand, which helps avoid the risks of overproduction and excess inventory.
- Continuous Improvement: Encourage and maintain a culture of continuous improvement by engaging employees in the problem-solving process and empowering them to suggest and implement changes themselves.
- Respect for People: Finally, Lean is about recognizing the importance of the people involved in a process and fostering a supportive, collaborative environment that values the knowledge, skills, and contributions they offer.
What is Six Sigma?
The Six Sigma methodology is a data-driven approach to process improvement that originated at Motorola in the 1980s and is now used in companies across industries. The term “Six Sigma” refers to the statistical measuring of process performance that represents a level of quality where the volume of defects is very low. Six Sigma employs multiple tools and techniques, including process capability analysis, root cause analysis, design of experiments (DOE), and statistical process control (SPC), to help businesses measure process variations, identify areas for improvement, and guide decision-making based on data-driven insights.
The critical components of Six Sigma are:
- Define the problem to address or the opportunity for improvement alongside the goals and objectives you want to achieve. This involves understanding the customer’s requirements and expectations for the project.
- Measure a process’s performance and identify improvement areas by collecting data. You can accomplish this with statistical tools and techniques that assess process capability and identify sources of variation.
- Analyze the collected data to identify root causes of defects, errors, or inefficiencies.
- Improve process performance by developing solutions that address the identified causes of inefficiencies.
- Control the mechanisms you implemented to sustain the improvements and ensure continued process stability. This involves implementing monitoring systems, creating standard operating procedures, and training personnel to maintain desired performance.
What’s the Difference Between Lean and Six Sigma?
While Lean and Six Sigma share the goal of improving company efficiency, they use different principles to achieve that objective. For example, the Lean methodology focuses on analyzing various workflows to reduce cycle times and eliminate waste, aiming to maximize value for the customer. Meanwhile, Six Sigma uses a data-driven method called DMAIC (Define, Measure, Analyze, Improve, Control) to identify and eliminate the causes of defects or errors in a process.
These methodologies have different scopes and focus areas but can be combined (becoming Lean Six Sigma) to achieve comprehensive process improvement. The difference in goals between Lean and Six Sigma comes down to this: Lean focuses on optimizing processes by eliminating waste (i.e., increasing flow), while Six Sigma focuses on improving operations by reducing process variation (i.e., maximizing consistency). It’s a subtle but crucial distinction, as both approaches have the same goal (improving company processes) but distinct ways of achieving it.
So, What’s Lean Six Sigma?
Now that we’ve established a baseline for Lean and Six Sigma, let’s look at what they can do when combined. By integrating the principles of tools of Lean and Six Sigma, this practice combines the waste reduction and flow optimization principles of Lean with the data-driven problem-solving and statistical analysis techniques of Six Sigma. Together, these methodologies empower organizations with the tools, concepts, and guidelines they need to fast-track their process improvement efforts.
NOW READ: The Best Lean Six Sigma Books for Professionals to Consider