Understanding the Difference: ERP vs. MRP
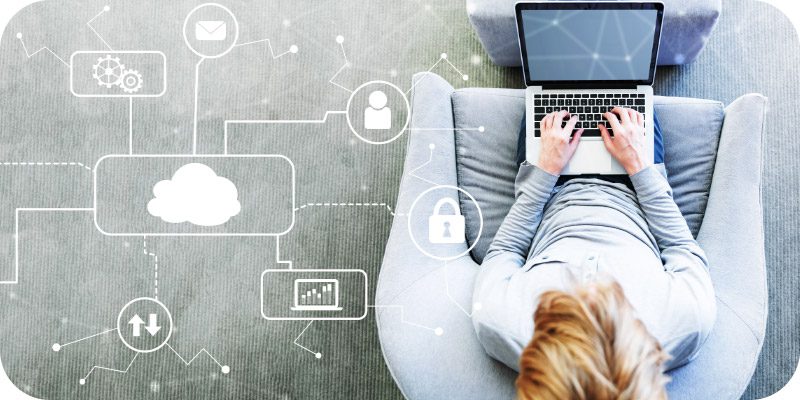
When it comes to manufacturing technology, the terms ERP and MRP inevitably come to mind. The two acronyms sound so similar that they are often mistaken as being the same thing. However, Enterprise Resource Planning (ERP) and Material Requirements Planning (MRP) are two very different systems. Each have their own advantages, use cases, and even disadvantages.
Widget not in any sidebars
What is ERP?
ERP refers to the systems and software packages used by organizations to manage day-to-day business activities, such as accounting, procurement, project management, sales, and manufacturing and/or distribution operations. Through its set of modules, ERP systems integrate all the core processes of a business into one single system. By doing so, ERP systems eliminate data duplication and provide data integrity with a “single source of truth.”
An ERP system also has the ability to automate the business, enables generation of synchronized reports on key business metrics, streamlines the processes, and improves overall business productivity. Today, ERP systems are critical for managing thousands of businesses of all sizes and in all industries.
What is MRP?
An MRP system can be defined as a tool that helps the manufacturers plan for the materials they are likely to need for production, when they might need it, and in what quantity they will need it. Unlike an ERP software, a material requirements planning system is exclusively used to help manage manufacturing processes, as businesses use this software to plan their production, calculate the raw material quantity required, forecast, and order raw materials. This way, they have the right material available in the right quantity at the right time and on right date for production.
As standalone system, MRP predominantly deals with the inventory management & production scheduling areas of the business. However, MRP is also typically one of many modules of an ERP software.
Benefits of ERP
Strategic Planning
ERP software can pick out the areas where improvements are needed and necessary. As a result, it can enhance the overall effectiveness and efficiency of the organization, especially when it comes to time management. Once the problems have been detected, it’s easier to monitor whether the changes that will be made will be effective or not. It also reduces costs and risks because it streamlines different business processes, which in turn reduces the operational and management costs. Whereas, improved data integrity and financial control reduce overall business risks.
In other words, integrating a powerful ERP solution helps reduce a business’s labor and operating costs. With it, businesses can better manage their time and entrepreneurial resources, eventually saving their money and seeing maximum ROI. It also allows them to consolidate their financial reporting and other costs (like administration).
Operational Efficiency
Regardless of where you create, fabricate, and deliver products, the need for integrated operations is always intrinsic to the manufacturing sector. Today’s global interest in making something in one country, then selling that product everywhere else in real-time is only growing. In the past, this beehive of coordination required enormous amounts of intellectual, operational, and financial ‘sweat’ just to ensure that raw materials always arrived at the right places at the right time. However, with today’s ERP systems, this flurry of headaches are mitigated, and in some cases, eliminated entirely; since ERP platforms allow everyone in the production chain, whether big or small, to talk and interact with each other as necessary across a common digital playing field.
A successful and competent ERP solution uses an integrated centralized database that supports all core processes of a business. This leads to the effortless integration of silo departments and processes within the entire organization. Having seamless integration within an organization allows for greater sharing of ideas, coherent decision-making and improves customer experiences. It also helps with informed (and better) decision making.
Benefits of MRP
Increased Inventory Management
Improving stock and inventory management are often big incentives that have motivated a number of manufacturers to implement MRP software. MRP may be a standalone system, but it functions by itself with only manufacturing-related features. Inventory control, stock movements, stock lot and serial number tracking, shipments and much more are all taken care of with an MRP platform. By optimizing inventory levels, it lets manufacturers know which raw material is required for production, how much of it is needed, and from where can it be purchased.
Accurate Material Planning and Purchasing
Purchase planning requires a smart system to track the production steps and identify any needed purchases while counter-checking with the production schedule and expected material deliveries. By increasing the accuracy of inventory management (having what’s needed, when needed, and available for production) manufacturing businesses can successfully manage vendors, purchase terms are centrally managed- including delivery and cost terms, and accessible when planning production – purchase requests can be quickly fulfilled after the customer order is received, and all steps of manufacturing and the availability of materials is monitored.
Looking for more? Download our Enterprise Resource Planning Buyers Guide for free to compare the top-24 products available on the market with full page vendor profiles, key capabilities, an ERP software market overview, our bottom line analysis, and questions for prospective buyers.
And don’t forget to follow us on Twitter, Facebook and LinkedIn for all the latest in the ERP space!