An Example AI Readiness Assessment Framework for Manufacturing Companies
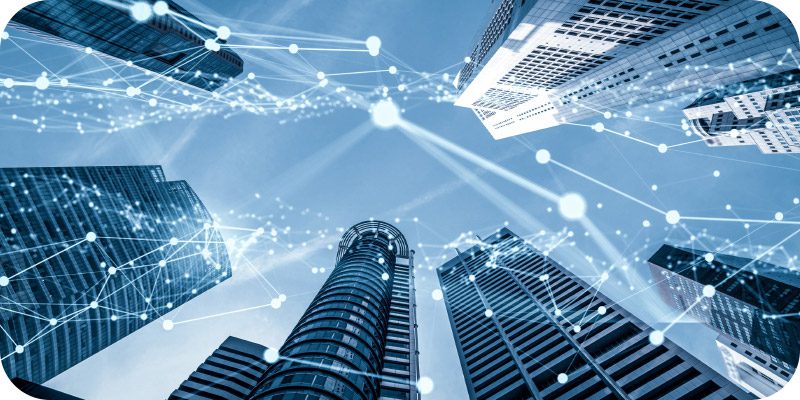
To help companies remain competitive amidst changing markets, the Solutions Review editors have outlined an example AI readiness assessment framework for manufacturing companies to use as they work toward AI adoption.
Manufacturing companies are facing unprecedented pressure to implement AI systems. The industry has always been a poster child for advanced technologies—look at how industrial automation revolutionized the sector in the 1950s—but the rise of AI seems poised to eclipse it entirely. However, implementing AI is easier said than done, especially since manufacturers must maintain operational excellence, regulatory compliance, and competitive positioning during the implementation.
Most AI readiness assessments fail manufacturing organizations because they apply generic frameworks designed for service industries or technology companies. Manufacturing requires specialized evaluation criteria that account for physical production constraints, supply chain complexity, safety requirements, global concerns, and the unique interplay between human expertise and automated systems.
That’s what this framework aims to provide, as it outlines a comprehensive assessment methodology specifically calibrated for manufacturing environments. This will help teams address the distinctive challenges of integrating AI into production systems, quality control, predictive maintenance, and operational optimization.
Core Assessment Dimensions
Production System Integration Readiness
Manufacturing AI implementations must interface with existing production control systems, often requiring real-time decision-making capabilities that service-sector AI applications rarely encounter. The assessment begins with evaluating the compatibility of the Manufacturing Execution System (MES), the potential for Supervisory Control and Data Acquisition (SCADA) integration, and the readiness of the Enterprise Resource Planning (ERP) system for AI-driven insights.
Critical evaluation points include data flow architecture between production systems, latency requirements for real-time AI decision-making, and the ability to implement AI recommendations without disrupting established production sequences. Manufacturing systems typically operate on deterministic schedules with tight tolerances, making AI integration significantly more complex than administrative or customer service applications.
A well-designed framework will examine whether current system architectures can support bi-directional data exchange, real-time inference capabilities, and fail-safe mechanisms that prevent AI-driven decisions from compromising production safety or quality standards. This includes assessing the robustness of existing communication protocols, data validation procedures, and exception handling capabilities within the manufacturing technology stack.
Operational Technology Security Posture
Manufacturing environments present unique cybersecurity challenges that differ substantially from traditional IT security frameworks. Operational Technology (OT) networks often contain legacy systems with limited security features, creating vulnerability vectors that AI implementations can inadvertently exploit or expand. One area companies should assess is network segmentation between IT and OT environments, which covers air-gapped system protection and the security implications of introducing AI-enabled data collection and processing capabilities. Manufacturing AI systems frequently require access to production data, sensor readings, and control system parameters representing critical intellectual property and operational vulnerabilities.
Particular attention focuses on evaluating Industrial Internet of Things (IIoT) device security, edge computing security protocols, and the potential for AI systems to create new attack vectors through expanded data access requirements. The framework assesses whether organizations can implement AI solutions while maintaining compliance with industrial security standards and protecting against cyber and physical threats.
Data Quality and Availability Assessment
Manufacturing generates vast data sets, but much of this information exists in formats, systems, and contexts that resist straightforward AI implementation. Before implementing AI, a manufacturer’s readiness assessment should evaluate data completeness, accuracy, temporal consistency, and semantic coherence across production systems.
Manufacturing data presents unique challenges, as it encompasses factors like sensor drift, calibration inconsistencies, maintenance-related data gaps, and the complex relationships between process parameters and quality outcomes. Unlike transactional business data, manufacturing information often requires domain-specific preprocessing, cleaning, and contextualization before AI algorithms can extract meaningful insights.
Assessments should examine data governance practices, standardization procedures, and the availability of historical data sufficient for model training and validation. Manufacturing AI applications typically require extensive historical datasets that capture seasonal variations, equipment aging effects, and process optimization cycles that may span months or years.
Human Capital and Change Management Readiness
Manufacturing organizations often maintain deeply embedded expertise in production processes, quality control, and equipment operation that AI systems cannot easily replace. The framework evaluates how effectively organizations can integrate AI capabilities with existing human expertise rather than attempting to replace skilled operators and technicians wholesale. Assessment criteria for this area include:
- The willingness of production staff to work alongside AI systems.
- The availability of personnel capable of maintaining and troubleshooting AI implementations.
- The organizational capacity to retrain workers for AI-augmented roles.
Manufacturing environments typically require specialized knowledge that combines theoretical understanding with practical experience gained through years of hands-on operation, and the human capital assessment must reflect that reality. This can take the form of examining whether organizations can develop hybrid human-AI workflows that leverage the strengths of both artificial and human intelligence, particularly in areas requiring judgment, creativity, and adaptation to unexpected circumstances that frequently arise in manufacturing environments.
Technical Infrastructure Evaluation
Edge Computing and Real-Time Processing Capabilities
Manufacturing AI applications frequently require real-time or near-real-time processing capabilities that not every solution can reliably provide. Network latency, connectivity interruptions, and bandwidth limitations can severely compromise AI system effectiveness in production environments, requiring manufacturers to evaluate their existing edge computing infrastructure, local processing capabilities, and the ability to implement AI inference at the point of data generation. Another point to consider is that manufacturing environments often require AI systems that can operate independently of external connectivity while maintaining synchronization with broader organizational systems.
Critical evaluation points include local storage capacity for AI models and training data, processing power sufficient for real-time inference, and redundancy mechanisms that ensure continued operation during network or system failures. The framework assesses whether organizations can implement distributed AI architectures that balance local responsiveness with centralized coordination and control.
Sensor Integration and Data Collection Infrastructure
Manufacturing AI systems depend on comprehensive, accurate, and timely data collection from production processes. As such, assessments must assess existing sensor networks, data acquisition systems, and the potential for expanding data collection capabilities to support AI implementations. This can be complicated by environments that contain a mixture of legacy sensors, modern digital instruments, and hybrid systems that require different data collection approaches, all common in manufacturing.
To that end, a manufacturing-centric AI readiness framework examines whether current sensor infrastructure can provide the data quality, quantity, and temporal resolution required for successful AI model training and operation. Particular attention focuses on evaluating sensor calibration procedures, data validation mechanisms, and the ability to integrate data from disparate sources into coherent datasets suitable for AI processing.
Model Deployment and Maintenance Infrastructure
Manufacturing AI systems requires specialized deployment and maintenance procedures that account for production schedule constraints, safety requirements, and the need for continuous operation. Assessments evaluate the organizational capacity to implement, monitor, and update AI models within manufacturing environments. Critical evaluation points include:
- The ability to test AI models in production environments without disrupting operations
- Procedures for validating model performance against manufacturing outcomes.
- Mechanisms for updating models based on changing production conditions.
Manufacturing environments often require AI systems that can adapt to equipment modifications, process changes, and evolving quality requirements, so organizations should identify whether they can implement the model versioning, rollback capabilities, and performance monitoring systems that ensure AI implementations continue to deliver value over time.
Domain-Specific Readiness Factors
Quality Control and Statistical Process Control Integration
Manufacturing quality control systems often rely on Statistical Process Control (SPC) methodologies refined over decades of industrial practice. AI implementations must integrate with existing quality frameworks while enhancing rather than replacing proven statistical methods. Additionally, manufacturing quality control typically requires explainable AI approaches that can provide a clear rationale for quality decisions and recommendations.
Readiness assessments will explore how effectively an organization can combine AI-driven quality predictions with traditional SPC approaches, maintaining compliance with industry quality standards while leveraging AI capabilities for early defect detection and process optimization. Evaluation points include:
- The ability to maintain traceability between AI-driven quality decisions and final product outcomes.
- Integration with existing quality management systems.
- Compliance with regulatory requirements that may mandate specific quality control procedures.
Frameworks must assess whether organizations can implement AI quality control systems that enhance rather than compromise existing quality assurance processes.
Predictive Maintenance and Asset Management Readiness
Manufacturing equipment maintenance represents one of the most promising applications for AI technology, but successful implementation requires a sophisticated understanding of equipment behavior, failure modes, and maintenance practices. The assessment evaluates organizational readiness to implement AI-driven predictive maintenance while maintaining existing preventive maintenance programs.
Frameworks will examine whether organizations can collect and analyze the diverse data types required for effective predictive maintenance, including vibration analysis, thermal imaging, oil analysis, and operational parameter monitoring. Manufacturing predictive maintenance AI systems must account for the complex relationships between equipment condition, production demands, and maintenance scheduling constraints. This entails evaluating the availability of historical maintenance data, the ability to correlate equipment condition with production quality outcomes, and the organizational capacity to act on AI-generated maintenance recommendations.
Supply Chain and Inventory Optimization Readiness
Manufacturing supply chain management involves complex interdependencies between material availability, production scheduling, quality requirements, and customer demand patterns. AI implementations must account for these relationships while providing actionable insights for inventory optimization and supply chain coordination. This includes evaluating the availability of supply chain data, the ability to integrate AI recommendations with existing planning systems, and the organizational capacity to implement dynamic inventory management based on AI-driven demand forecasting.
Evaluation points include the ability to model supply chain disruptions, integrate AI recommendations with production planning systems, and maintain appropriate inventory levels while minimizing carrying costs. The framework assesses whether organizations can implement AI-driven supply chain optimization that enhances rather than disrupts existing supplier relationships and procurement processes.
Implementation Readiness Assessment
Pilot Project Selection and Validation Framework
Manufacturing AI implementations benefit from carefully selected pilot projects that demonstrate value while minimizing risk to production operations. For this phase of the assessment framework, manufacturers will explore their capacity to identify, implement, and validate AI pilot projects within manufacturing environments. Effective pilot project selection requires balancing potential AI benefits against implementation complexity, data availability, and the ability to measure success using manufacturing-specific metrics.
Industry-specific AI pilots typically require more extensive validation procedures than applications in other industries due to the potential consequences of incorrect predictions or recommendations. As such, the most relevant points to assess include the ability to isolate pilot project variables, measure AI impact on manufacturing outcomes, and scale successful pilot implementations across broader production systems.
Regulatory Compliance and Industry Standards Alignment
Manufacturing industries often operate under strict regulatory requirements that govern product quality, safety procedures, and environmental compliance. Like the World Economic Forum explains, “the convergence of ethical principles with AI deployment becomes imperative to ensure responsible innovation and sustainable progress.” This is especially crucial for manufacturers, who must maintain compliance with existing regulations while potentially enabling enhanced compliance monitoring and reporting capabilities.
Assessments should evaluate how AI implementations interact with these regulatory requirements, covering audit trails for AI-driven decisions and the organizational capacity to demonstrate compliance with industry standards. Specific points to examine include the ability to maintain regulatory compliance during AI adoption, the potential for AI systems to enhance compliance monitoring, and the organizational capacity to adapt AI implementations to evolving regulatory requirements.
Vendor Selection and Partnership Evaluation
Manufacturing AI implementations often require specialized vendors with an extensive understanding of manufacturing processes, equipment, and operational constraints. The assessment evaluates organizational capacity to select and manage AI vendor relationships within manufacturing contexts. For example, an effective vendor selection requires balancing AI technical capabilities with manufacturing domain expertise, implementation experience, and long-term support capabilities.
Assessments should examine whether organizations can identify vendors capable of delivering AI solutions that integrate effectively with existing manufacturing systems and processes. For example, priorities in readiness assessments include vendor experience with manufacturing AI implementations, the ability to provide ongoing support and maintenance, and the alignment between vendor capabilities and organizational AI objectives.
Maturity Assessment and Progression Framework
Foundational Readiness Level
Organizations at the foundational level possess basic data collection capabilities, established quality control procedures, and general awareness of AI potential within manufacturing contexts. Manufacturers require significant infrastructure development and capability building before implementing production AI systems. Enterprises should focus on improving data quality and availability, establishing basic analytics capabilities, and developing an organizational understanding of AI applications within manufacturing environments.
Progression paths emphasize building technical infrastructure and human capabilities that support future AI implementations. Additionally, manufacturing organizations at this level may benefit from focusing on Industry 4.0 initiatives that create the data infrastructure necessary for eventual AI implementation, rather than attempting direct AI deployment.
Intermediate Readiness Level
Intermediate organizations possess established data collection and analysis capabilities, more experience with automation technologies, and some pilot AI implementations within manufacturing contexts. These organizations typically require focused development in specific AI application areas and integration capabilities. These organizations should focus on expanding successful pilot implementations, developing specialized AI capabilities for manufacturing applications, and building organizational expertise in AI system management and maintenance. The progression path for these organizations emphasizes scaling existing capabilities and developing specialized manufacturing AI expertise.
Advanced Readiness Level
Advanced organizations possess comprehensive AI capabilities, established manufacturing AI implementations, and organizational cultures capable of integrating AI insights into production decision-making. Because of these capabilities, advanced-level organizations typically focus on optimizing existing AI systems and exploring advanced AI applications.
At this stage, manufacturers should focus on developing cutting-edge AI capabilities, exploring emerging AI technologies, and sharing expertise with industry partners and suppliers. The progression path emphasizes innovation, optimization, and leadership in manufacturing AI implementation.
Conclusion
Manufacturing AI readiness requires specialized assessment approaches that account for the unique challenges and opportunities within production environments. This framework provides a comprehensive methodology for evaluating organizational readiness while recognizing the distinctive requirements of manufacturing AI projects.
Successful manufacturing AI initiatives require careful integration with existing production systems, comprehensive data quality management, and organizational cultures that effectively combine human expertise with AI capabilities, which a properly configured AI readiness assessment framework can provide. When manufacturers carefully assess their readiness and develop targeted improvement strategies, they will be better positioned to realize the substantial benefits that AI can provide within manufacturing contexts.